What nearshoring and reshoring means for recruitment in the logistics industry
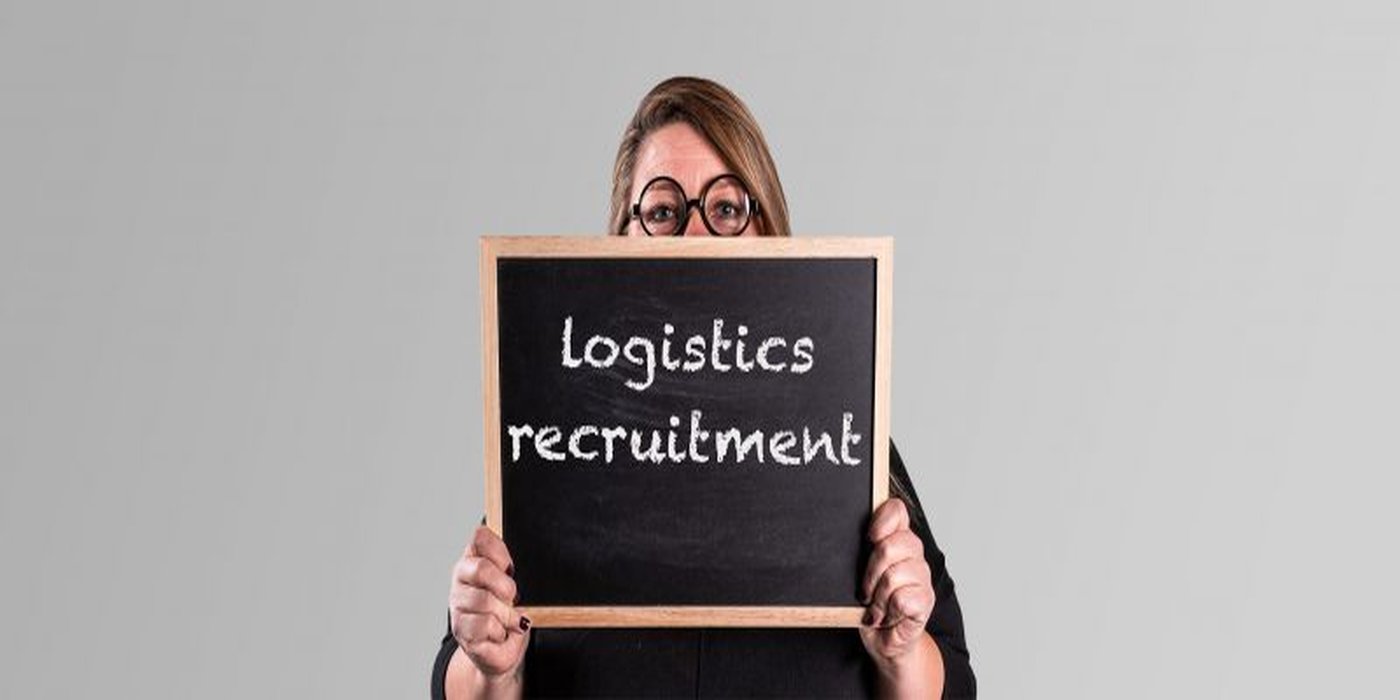
The last few years have been unprecedented for the logistics industry. Admittedly, they’ve been unprecedented for everyone, but the logistics industry has seen some of the biggest changes in living memory.We’ve certainly never seen so many people concerned about logistics and supply chains. From being the concern of production managers and logistics firms, we’re now seeing articles expressing concern about logistics issues in all of the major newspapers.From food to fuel and laptops to Lamborghinis, people are starting to think more about where their goods come from and whether they can get them when needed.It’s not just a question of publicity. Brexit and the pandemic have been once-in-a-generation events that have dramatically shifted the ground under logistics companies’ feet.All this upheaval hasn’t brought many apparent benefits for logistics companies. Brexit has increased costs and delays. The pandemic increased demand but made it harder to meet that demand.These dramatic events must be a catalyst for change if we want our companies to survive. UK businesses have to change how they operate to maintain their competitive advantages (and happy customers).We’ve already talked a little about how Brexit impacted the logistics sector. In this article, we’re going to look at some of the important ways British businesses are adapting to the rapidly changing landscape; nearshoring and reshoring.We’re going to talk about what nearshoring and reshoring are, why they’re important, and what they mean for recruitment within the logistics sector.
What is nearshoring and reshoring?
Over the last 50 years, companies in the developed world have been keen to offshore much of their unskilled labour. They’ve built factories in countries like India and China, secure in the knowledge that cheap labour costs made this a good investment, even taking subsequent shipping into account.Brexit and the pandemic both demonstrated the risks of offshoring. Global crises create challenges for international logistics, and the just-in-time production model doesn’t provide much leeway when things go wrong.
Reshoring is the growing practice of bringing manufacture, production, and even services back into the same country as the main company. For UK companies, this would mean moving most or all of their production back into the UK.Nearshoring offers a middle ground between onshoring and reshoring. This is when a company moves their production to another country, but one that is geographically close to the main company.In terms of UK companies, nearshoring would typically involve moving production to parts of the EU, like the Czech Republic or Poland… though Brexit has complicated some of these decisions.
Reshoring and nearshoring offer significant advantages to offset the increased labour costs and expenditure associated with moving production across continents.Communication and collaboration are often significantly easier when working with colleagues in a similar time zone. This can help improve day-to-day efficiency and facilitate crisis management when things go wrong.Reshoring and nearshoring also offer advantages for quality assurance and customer confidence. Fairly or not, consumers strongly perceive that goods made in the UK or EU are likely to be of higher quality than those from more distant countries.One of the biggest advantages for many companies of nearshoring or reshoring is the reduction in delivery times and the associated reduction in risk.
The huge delays following the grounding of the Ever Given in the Suez Canal highlighted vulnerabilities in global supply chains. Since then, companies are increasingly uncomfortable with potential delays and shortages.It’s not just the risk of delays that’s driving companies towards reshoring. The dangers of political, economic, and logistical upheaval have become real in a way that they weren’t before. Major geopolitical changes, such as leaving the single market, simply weren’t factored into most companies’ long-term planning. Reshoring, in particular, insulates companies against such unexpected circumstances. Nearshoring and reshoring increase resilience, an essential quality in unpredictable times.
What does this mean for logistics recruitment?
If more UK organisations are moving their production back to the UK, this will significantly affect logistics companies. To adapt, we will have to change how we do business and who we hire.With more reshoring, UK-based logistics companies will see heightened demand for in-country logistics and logistics management professionals in particular. Logistics firms will probably have to either take on new staff with experience in in-country logistics or upskill existing workers. Fewer staff with international skills will be required, but companies will need exceptional workers to fill that niche.
Team members who can navigate post-Brexit paperwork with ease will become highly sought-after.If reshoring becomes commonplace, companies across the board will be looking to hire more workers. This will likely lead to higher salaries and higher costs for companies. Logistics firms are not immune from these rising costs.Increasing technology and digitisation are also having an impact on payroll costs. Where companies once outsourced low-cost, low-skill roles, they’re typically bringing back high-skilled positions. They require tech-savvy staff to fill them.The same will be true of the logistics industry. Companies need to find highly-skilled, experienced workers to carry out the complex tasks required for managing in-country logistics. Soft skills will also be in high demand, with adaptable staff with great communication skills being able to command a premium.
Meeting your logistics recruitment demands
Recruitment is difficult across the board right now. With so many changes taking place in the logistics sector, there are likely to be particular challenges facing companies trying to find new, skilled logistics staff.Taking the right steps now can help you avoid future recruitment problems. Taking a deep look at your processes for hiring and retaining great staff lets you identify where to devote your efforts.The more streamlined your recruitment processes (from application to onboarding), the more successful you are likely to be in attracting great candidates. Increasing automation in your recruitment processes can really help with this.Considering your employer branding is another important measure companies can take to ensure you’re getting the best applicants for your open roles.Logistics firms are also going to need to look to younger workers.
Gen Z has different expectations of employers than previous generations. They’re looking for companies who understand the importance of diversity, equity, and inclusion. Companies will need to look carefully at their job adverts to attract these workers and consider making a public DEI statement, for example. Logistics firms devoting extra effort to their gender balance may be particularly successful.You might be facing a challenging time in logistics recruitment, but you don’t have to face it alone.